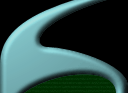 |
 |
|
The Dragoon rocket is about 15 feet tall and 9 inches in diameter. The liftoff weight is about 450 pounds with the solid rocket motor weighing about 250 pounds. For the first mission, the rocket will fly to an altitude of about 350,000 feet or 66 miles. NASA defines space at about an altitude of 58 miles, so for this flight, our destination will be space! When the rocket motor burns out, the Dragoon rocket will be going 4,000 miles per hour, or 6 times the speed of sound. After reaching space and conducting several experiments, the rocket will return and be recovered with a parachute recovery system.
The nosecone is made from three pieces of aluminum with a 6 inch tip made of steel. The steel tip is needed to absorb the heat generated from the shock wave in front of the rocket. The rest of the nosecone is made from aluminum to reduce its weight. The payload section is made from aluminum and is 18 inches long and about 9 inches is diameter. We have room for a 12 inch long payload, but longer payloads can be accommodated via special request. The suborbital configuration rocket can launch up to 22 pounds of weight to altitudes approaching 200 miles.
We need to separate the vehicle components during the flight to eject the recovery systems. The separation system is designed as a pressure cartridge and retaining pins. The pressure cartridge releases gases that will shear the nylon retaining pins with a simple cutting technique. Designed as a simple, yet robust system, the device assures separation through simplicity.
The recovery system is a two-stage system. The first stage is a guide surface drogue parachute that stabilizes the rocket until it reaches a low enough altitude that a larger parachute can be deployed. The larger parachute slows the rocket down much more and will allow the rocket to be recovered. Another advantage of a two-stage system is that it will reduce the amount of area that we need to launch and recover the rocket.
The motor for the Dragoon rocket is a solid rocket motor. This means that all the chemicals that provide the energy for the flight of the rocket are stored in solid form, not liquid form. This greatly reduces the amount of pre-flight preparation and simplifies the ground support equipment that we need. The rocket propellant feels like a rubber, much like the bottom of your tennis shoe. The motor casing must be able to withstand great pressure and is made from 6061 T6 aluminum. The motor is assembled in a cartridge loading method with closures and screw-in retainers to hold the entire motor together. The nozzle for the rocket motor is made from graphite; the properties of graphite make it very resistant to the extreme conditions inside the rocket motor.
There are four fins on the rocket to give it static stability. They are made from 3/8 inch thick aluminum with each of fins weighing about 6 pounds. The fins provide stability for the rocket, which makes it fly where we want it to go. The fins are angled very slightly, so the rocket will spin during its flight. This spinning gives the rocket dynamic stability and makes the rocket more resistant to disturbing affects during its flight.
|
|
|
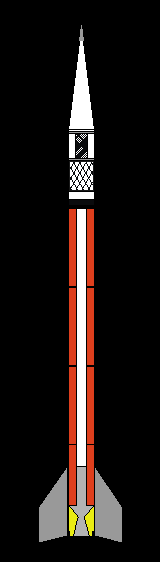 |
|
|